Turbines
Measurement of turbine blade temperatures is challenging for a number of reasons. The most obvious is optical access to the blades is limited, but the difficulties presented by the emissivity are formidable. The emissivity of the blades is complicated by a number of factors: the blades are metal, so the emissivity may change with wavelength. They may have a thermal barrier coating applied: emissivity of these materials is not well characterized. The blades present different geometries to the measuring instrument as they rotate, and this affects the energy radiated into the instrument’s acceptance angle. Soot coatings have also been observed on the blades, and these affect the emissivity; soot is most often present at startup and has been observed to burn off as the engine warms. This, of course, changes the emissivity.
The temperature for the uncooled second stage blades in a stationary turbine engine was measured as a function of operating conditions. An optical probe with a field of view perpendicular to its axis was used for this work. An inspection port about 2 inches upstream of the blades provided access for the periscope-type probe. The probe was armored and shielded to withstand the gas flow. Fiberoptic cabling to the probe was run in copper tubing and cooled with compressed air because of the elevated temperature in the immediate vicinity of the engine. An FMP2 SpectroPyrometer was modified to measure temperatures down to 635°C (1175°F), as the expected temperatures were around 700°C (1290°F).
The results of the measurement, presented below, showed that blade temperature changed for each operating condition. The four operating conditions were start up, base load, base load plus 20%, and base load minus 20%. The tolerance for all the data shown averaged 0.3%, indicating excellent accuracy.
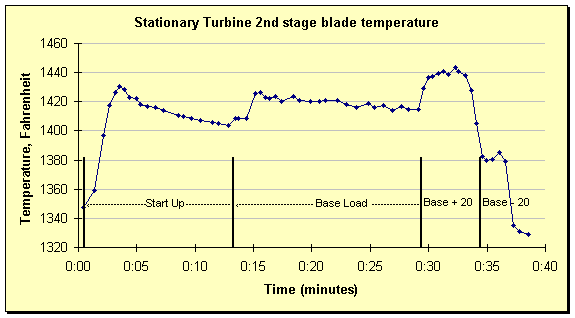
Turbine temperatures measured by an FMP2 SpectroPyrometer modified to improve low temperature response.