Investment Casting
Click here for a video of an investment casting run from cold charge to pour (12 MB). SpectroPyrometer real-time temperature and tolerance are graphically superimposed.
It is understandable that this industry takes a somewhat jaundiced view of pyrometry. It presents substantial problems to traditional pyrometry: the targets are molten, they are metallic in composition, and there are many of them (a bookkeeping issue – how to keep all those emissivities straight). The following results are an example taken from an extensive campaign of an expert system FAR SpectroPyrometer in an investment-casting application.
As a test, a solid charge was loaded in a furnace and heated to melting. A conventional pyrometer and the SpectroPyrometer monitored temperature. Several power adjustments were made to exercise the pyrometers. Then the charge was allowed to cool naturally. The results below are from the SpectroPyrometer.
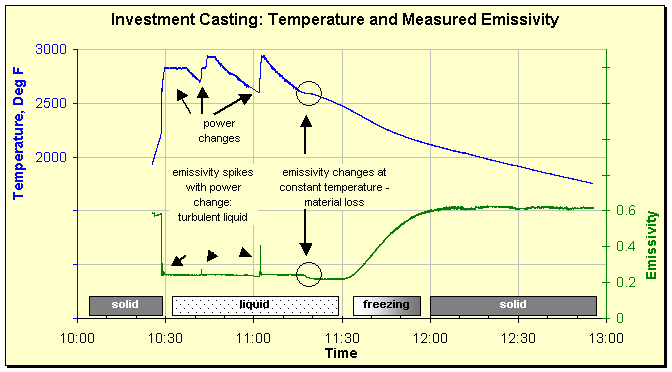
SpectroPyrometer’s results for temperature and emissivity for a non-ferrous alloy: emissivity changes with turbulence, time, and phase. This alloy is one of tens of alloys that may be run in the casting plant.
The conventional casting pyrometer’s results were compared to those of the SpectroPyrometer. The instrument in use was a brightness (single-color) pyrometer, set to an emissivity of 0.3. The instrument was in error by several hundreds of degrees, and the error changed from below actual temperature to above as emissivity changed. The tolerance determined by the SpectroPyrometer (the on-line accuracy) is also shown.
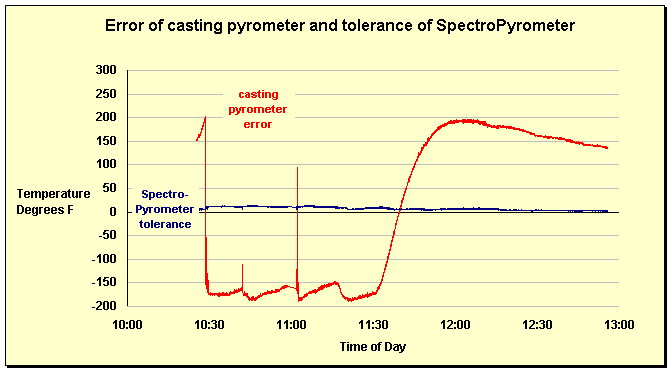
Error of a pyrometer with operator-set emissivity as material emissivity ranges between 0.22 – 0.60 contrasted with tolerance of SpectroPyrometer. Error was calculated by subtracting the actual temperature, as measured by the SpectroPyrometer, from the temperature yielded by the casting pyrometer.
We see that large errors result even though the operators followed the standard instructions given by pyrometer manufacturers. For targets of unknown emissivity, the user is often counseled to aim the pyrometer at the target and measure the temperature in some other way. Then, they are further instructed to twiddle the emissivity knob until the pyrometer temperature agrees with the other measuring technique. This methodology requires a significant investment of time and effort, and it works only rarely. Emissivity varies with too many parameters.
Advantages of Accurate Temperature
What does the vast improvement in temperature measurement mean to you? Consider the following results: the graphs reproduced below are from production cycles of an aerospace investment casting application; the controlling pyrometer is the key difference between them. Each graph shows both the temperature (blue) and emissivity (red) measured by a FAR SpectroPyrometer. Each contiguous temperature/emissivity cycle is one casting, resulting in several finished parts. Four consecutive castings are shown, and they are representative of the entire run in each case.
As is evident in the first graph with the conventional pyrometer controlling, the temperature is quite high, about 200 degrees hotter than the setpoint (just as the error shown above predicts). The temperature is not stable during heat up, and the maximum temperature is not repeatable. The emissivity tells a very interesting tale. The spikes are the result of severe electromagnetic stirring; the sequence goes like this: the conventional pyrometer sees an over-temperature value because the turbulence in the melt enhances the emissivity. In response, the controller turns off the power. The turbulence vanishes when the power is removed, and an under-temperature is then sensed by the pyrometer. The power is turned back on, and the resultant current surge violently stirs the melt. The cycle repeats, as can be seen in the spiky red trace. The violent stirring causes erosion of the refractory wall and hence inclusions in the product.
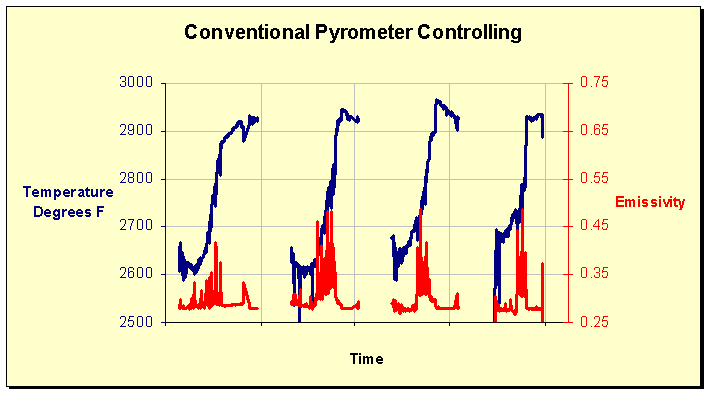
Conventional pyrometer controlling, SpectroPyrometer measuring temperature and emissivity for four casting cycles.
Contrast this behavior with that in the next graph when a SpectroPyrometer controls the process. The emissivity scale is the same, the temperature increments are the same, but the temperature range is lower. The reason for this is the process is now accurately achieving the setpoint temperature because of the accurate measurement of the SpectroPyrometer. Note that the temperature trace smoothly reaches the setpoint and controls closely about it until each cycle ends.
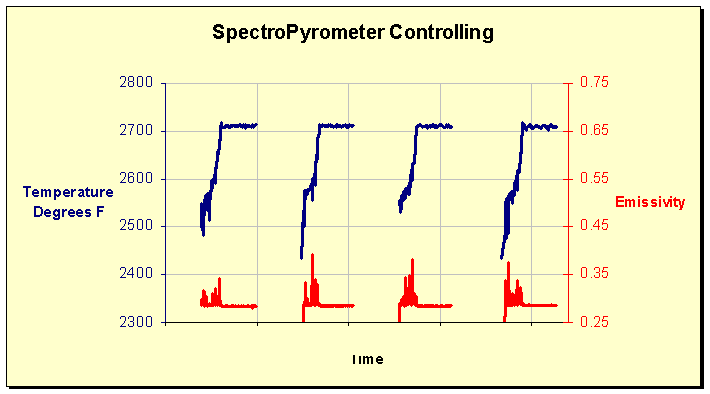
SpectroPyrometer measuring and controlling temperature for four casting cycles.
It is also evident that the spikiness, and therefore the turbulence of the melt, is greatly reduced. The repetitive power on-off sequence caused by and causing turbulence has been broken. There is still some turbulence from electromagnetic stirring of the melt during full power heatup, but this quiets completely when the setpoint is reached and power is reduced.
Several striking advantages are obvious: greater quality from reduced inclusions (from reduced refractory erosion), higher yield from faster casting cycles which reach the actual setpoint instead of an artificially high setpoint, lower maintenance costs from lower refractory erosion, and lower power costs from decreased power usage.
View a PDF of the data, emissivity, and error from the first example above on the same timeline (280 KB).